Explore D-85 (powerful) & D-35 (compact) neodymium fishing magnets
Unlocking Underwater Treasures: A Deep Dive into Fishing Magnets D-85 and D-35
Magnet fishing has rapidly grown from a niche hobby into a popular outdoor activity, offering the thrill of discovery and the satisfaction of cleaning waterways. But to truly unlock the secrets hidden beneath the surface, you need the right tools. This blog post takes a closer look at two popular choices: the Fishing Magnet D-85 and the Fishing Magnet D-35, helping you decide which powerful neodymium magnet is best suited for your next underwater adventure.
What Are Fishing Magnets D-85 and D-35?
At their core, the D-85 and D-35 are highly powerful neodymium fishing magnets, designed for retrieving ferrous metal objects from rivers, lakes, canals, and wells. The “D” in their names typically refers to their diameter in millimeters – D-85 is an 85mm diameter magnet, while D-35 is a more compact 35mm. This dimension is crucial, as it directly relates to the magnet’s pulling force and the types of objects it can retrieve.
Fishing Magnet D-85: The Heavyweight Champion
The D-85 fishing magnet is built for serious retrieval tasks. With its larger diameter (85mm), it boasts a significantly higher pulling force, often in the range of hundreds of kilograms (e.g., around 270 kg or more).
Key Features & Benefits of D-85:
Exceptional Pulling Power: Ideal for recovering larger, heavier items such as bicycles, safes, heavy tools, or even small engine parts.
Deep Water & Strong Currents: Its substantial strength makes it more effective in deeper waters or areas with stronger currents, where a lighter magnet might struggle to maintain grip.
Advanced Treasure Hunting: Preferred by experienced magnet fishers looking for significant finds or engaging in clean-up operations of substantial debris.
Durable Construction: Typically features multi-layer coatings (like Ni-Cu-Ni, Zinc, or Nickel) for enhanced rust resistance and longevity, crucial for frequent underwater use.
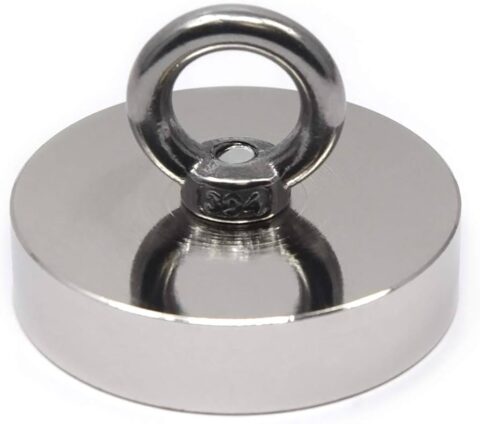
Fishing Magnet D-35: The Agile Explorer
The D-35 fishing magnet, with its smaller 35mm diameter, offers a different set of advantages, making it an excellent choice for beginners, casual enthusiasts, or specific retrieval scenarios. While its pulling force is lower (around 20-25 kg, depending on grade and design), it’s still remarkably strong for its size.
Key Features & Benefits of D-35:
- Portability & Ease of Use: Its compact size and lighter weight make it incredibly easy to transport, cast, and retrieve, perfect for spontaneous trips or for those who prefer a less strenuous experience.
- Targeting Smaller Objects: Excellent for picking up smaller items like keys, coins, fishing lures, screws, or other small metallic lost items.
- Ideal for Beginners: The manageable size and pull force make it a great starting point for newcomers to magnet fishing, allowing them to learn the ropes safely and effectively.
- Navigating Tight Spaces: Its smaller profile can be advantageous when trying to retrieve objects from confined areas, under docks, or between rocks.
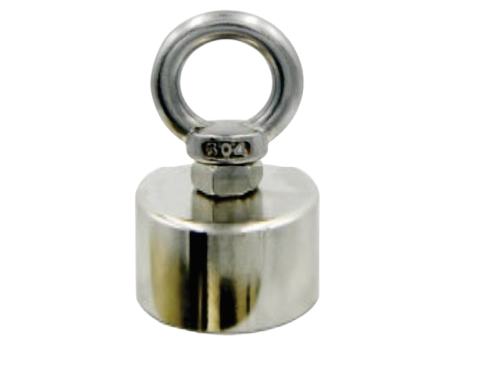
Common Ground: What Both D-85 and D-35 Offer
Despite their differences in size and power, both the D-85 and D-35 fishing magnets share fundamental characteristics that make them effective tools for underwater exploration:
Neodymium Core: Both are made from Neodymium (NdFeB), the strongest type of permanent magnet available, ensuring maximum pulling force for their respective sizes.
Versatility: Beyond treasure hunting, these magnets are valuable for retrieving lost tools in industrial settings, cleaning up metal debris from construction sites, or even aiding in scientific exploration.
Durability: Designed to withstand harsh underwater environments, often featuring protective coatings that resist corrosion and impact.
Kit Components: Many models come as part of a kit, including a high-strength rope, a sturdy carabiner for secure attachment, and protective gloves for safe handling.
Applications of Fishing Magnets
- Magnetic Fishing & Treasure Hunting: The most popular use, involving dropping the magnet into bodies of water to find historical artifacts, lost valuables, or interesting metal objects.
Lost Item Recovery: Accidentally dropped keys, tools, or other metallic items into a drain, well, or off a boat? A fishing magnet can be your best chance for recovery.
Waterway Cleanup: A fantastic way to contribute to environmental efforts by removing discarded metal waste from rivers, lakes, and oceans.
Safety First! Important Precautions
While incredibly fun and rewarding, magnet fishing with powerful neodymium magnets like the D-85 and D-35 requires extreme caution. These are not toys and their immense magnetic force can be dangerous if mishandled.
Keep Away from Electronics: Neodymium magnets can damage electronic devices, credit cards, and data storage.
Medical Implants: Individuals with pacemakers or other medical implants should never handle strong magnets.
Pinch Hazards: The magnetic force can cause severe pinches or crush injuries if fingers or skin get caught between the magnet and a metal object.
Controlled Environment: Always handle magnets in a controlled environment, away from unintended metal surfaces.
Children and Pets: Keep magnets strictly out of reach of children and pets.
Conclusion
Whether you opt for the robust pulling power of the Fishing Magnet D-85 for serious retrieval missions or the agile versatility of the Fishing Magnet D-35 for portable exploration, both magnets offer a gateway to exciting underwater discoveries. By understanding their unique strengths and adhering to safety guidelines, you’re well on your way to becoming a successful and responsible magnet fisher. Get ready to cast your line and see what treasures await!